鑄鋼件和鑄鐵件在生產(chǎn)和應(yīng)用過程中經(jīng)常會遇到各種問題,這些問題不僅影響鑄件的質(zhì)量,還會導(dǎo)致生產(chǎn)效率下降。本文將詳細分析鑄鋼件與鑄鐵件的常見問題,并提供相應(yīng)的解決方法,幫助讀者更好地理解和應(yīng)對這些問題。
一、鑄鋼件的常見問題及其解決方法
1.氣孔和夾渣
問題描述:鑄鋼件在澆注過程中容易產(chǎn)生氣孔和夾渣,導(dǎo)致鑄件表面和內(nèi)部存在缺陷。
原因分析:
澆注溫度過低:澆注溫度過低會導(dǎo)致金屬液流動性差,容易形成氣孔和夾渣。
澆注速度過快:澆注速度過快會導(dǎo)致金屬液沖擊砂模,產(chǎn)生氣孔和夾渣。
砂模透氣性差:砂模透氣性差會導(dǎo)致氣體無法及時排出,形成氣孔。
解決方法:
提高澆注溫度:確保澆注溫度在1500℃以上,提高金屬液的流動性。
控制澆注速度:合理控制澆注速度,避免金屬液沖擊砂模。
優(yōu)化砂模透氣性:選擇透氣性好的砂子,提高砂模的透氣性。
2.裂紋
問題描述:鑄鋼件在冷卻過程中容易產(chǎn)生裂紋,導(dǎo)致鑄件報廢。
原因分析:
冷卻速度過快:冷卻速度過快會導(dǎo)致鑄件內(nèi)部應(yīng)力增大,產(chǎn)生裂紋。
砂模強度不夠:砂模強度不夠會導(dǎo)致鑄件在冷卻過程中變形,產(chǎn)生裂紋。
熱處理不當:熱處理溫度和時間不合理,導(dǎo)致鑄件內(nèi)部應(yīng)力不均勻。
解決方法:
控制冷卻速度:通過調(diào)整冷卻介質(zhì)和冷卻時間,精確控制冷卻速度。
提高砂模強度:選擇強度高的砂子,提高砂模的強度。
優(yōu)化熱處理:合理設(shè)置熱處理溫度和時間,消除鑄件內(nèi)部應(yīng)力。
3.尺寸偏差
問題描述:鑄鋼件在加工過程中容易出現(xiàn)尺寸偏差,導(dǎo)致鑄件不符合圖紙要求。
原因分析:
模具尺寸精度不高:模具尺寸精度不高會導(dǎo)致鑄件尺寸偏差。
澆注過程控制不當:澆注過程中的溫度和速度控制不當,導(dǎo)致鑄件尺寸偏差。
冷卻過程控制不當:冷卻過程中的溫度和時間控制不當,導(dǎo)致鑄件尺寸偏差。
解決方法:
提高模具精度:通過三維建模和精密加工,提高模具尺寸精度。
嚴格控制澆注過程:合理控制澆注溫度和速度,避免尺寸偏差。
嚴格控制冷卻過程:合理控制冷卻溫度和時間,避免尺寸偏差。
4.表面粗糙
問題描述:鑄鋼件表面粗糙度較高,需要進行后續(xù)加工。
原因分析:
砂模表面粗糙:砂模表面粗糙會導(dǎo)致鑄件表面粗糙。
澆注過程控制不當:澆注過程中的溫度和速度控制不當,導(dǎo)致鑄件表面粗糙。
冷卻過程控制不當:冷卻過程中的溫度和時間控制不當,導(dǎo)致鑄件表面粗糙。
解決方法:
提高砂模表面質(zhì)量:選擇表面光滑的砂子,提高砂模表面質(zhì)量。
嚴格控制澆注過程:合理控制澆注溫度和速度,避免表面粗糙。
嚴格控制冷卻過程:合理控制冷卻溫度和時間,避免表面粗糙。
5.機械性能不足
問題描述:鑄鋼件在使用過程中機械性能不足,導(dǎo)致使用壽命縮短。
原因分析:
成分控制不當:鑄鋼成分控制不當,導(dǎo)致機械性能不足。
熱處理不當:熱處理溫度和時間不合理,導(dǎo)致機械性能不足。
冷卻過程控制不當:冷卻過程中的溫度和時間控制不當,導(dǎo)致機械性能不足。
解決方法:
嚴格控制成分:通過成分檢測,確保鑄鋼成分符合要求。
優(yōu)化熱處理:合理設(shè)置熱處理溫度和時間,提高機械性能。
嚴格控制冷卻過程:合理控制冷卻溫度和時間,提高機械性能。
二、鑄鐵件的常見問題及其解決方法
1.氣孔和夾渣
問題描述:鑄鐵件在澆注過程中容易產(chǎn)生氣孔和夾渣,導(dǎo)致鑄件表面和內(nèi)部存在缺陷。
原因分析:
澆注溫度過低:澆注溫度過低會導(dǎo)致金屬液流動性差,容易形成氣孔和夾渣。
澆注速度過快:澆注速度過快會導(dǎo)致金屬液沖擊砂模,產(chǎn)生氣孔和夾渣。
砂模透氣性差:砂模透氣性差會導(dǎo)致氣體無法及時排出,形成氣孔。
解決方法:
提高澆注溫度:確保澆注溫度在1200℃~1400℃之間,提高金屬液的流動性。
控制澆注速度:合理控制澆注速度,避免金屬液沖擊砂模。
優(yōu)化砂模透氣性:選擇透氣性好的砂子,提高砂模的透氣性。
2.裂紋
問題描述:鑄鐵件在冷卻過程中容易產(chǎn)生裂紋,導(dǎo)致鑄件報廢。
原因分析:
冷卻速度過快:冷卻速度過快會導(dǎo)致鑄件內(nèi)部應(yīng)力增大,產(chǎn)生裂紋。
砂模強度不夠:砂模強度不夠會導(dǎo)致鑄件在冷卻過程中變形,產(chǎn)生裂紋。
熱處理不當:熱處理溫度和時間不合理,導(dǎo)致鑄件內(nèi)部應(yīng)力不均勻。
解決方法:
控制冷卻速度:通過調(diào)整冷卻介質(zhì)和冷卻時間,精確控制冷卻速度。
提高砂模強度:選擇強度高的砂子,提高砂模的強度。
優(yōu)化熱處理:合理設(shè)置熱處理溫度和時間,消除鑄件內(nèi)部應(yīng)力。
3.尺寸偏差
問題描述:鑄鐵件在加工過程中容易出現(xiàn)尺寸偏差,導(dǎo)致鑄件不符合圖紙要求。
原因分析:
模具尺寸精度不高:模具尺寸精度不高會導(dǎo)致鑄件尺寸偏差。
澆注過程控制不當:澆注過程中的溫度和速度控制不當,導(dǎo)致鑄件尺寸偏差。
冷卻過程控制不當:冷卻過程中的溫度和時間控制不當,導(dǎo)致鑄件尺寸偏差。
解決方法:
提高模具精度:通過三維建模和精密加工,提高模具尺寸精度。
嚴格控制澆注過程:合理控制澆注溫度和速度,避免尺寸偏差。
嚴格控制冷卻過程:合理控制冷卻溫度和時間,避免尺寸偏差。
4.表面粗糙
問題描述:鑄鐵件表面粗糙度較高,需要進行后續(xù)加工。
原因分析:
砂模表面粗糙:砂模表面粗糙會導(dǎo)致鑄件表面粗糙。
澆注過程控制不當:澆注過程中的溫度和速度控制不當,導(dǎo)致鑄件表面粗糙。
冷卻過程控制不當:冷卻過程中的溫度和時間控制不當,導(dǎo)致鑄件表面粗糙。
解決方法:
提高砂模表面質(zhì)量:選擇表面光滑的砂子,提高砂模表面質(zhì)量。
嚴格控制澆注過程:合理控制澆注溫度和速度,避免表面粗糙。
嚴格控制冷卻過程:合理控制冷卻溫度和時間,避免表面粗糙。
5.機械性能不足
問題描述:鑄鐵件在使用過程中機械性能不足,導(dǎo)致使用壽命縮短。
原因分析:
成分控制不當:鑄鐵成分控制不當,導(dǎo)致機械性能不足。
熱處理不當:熱處理溫度和時間不合理,導(dǎo)致機械性能不足。
冷卻過程控制不當:冷卻過程中的溫度和時間控制不當,導(dǎo)致機械性能不足。
解決方法:
嚴格控制成分:通過成分檢測,確保鑄鐵成分符合要求。
優(yōu)化熱處理:合理設(shè)置熱處理溫度和時間,提高機械性能。
嚴格控制冷卻過程:合理控制冷卻溫度和時間,提高機械性能。
三、案例分析
以某機械制造企業(yè)的發(fā)動機缸體生產(chǎn)為例,該企業(yè)在鑄鋼件和鑄鐵件的生產(chǎn)過程中遇到了鑄件質(zhì)量不穩(wěn)定的問題。通過以下措施,企業(yè)解決了這些問題:
1.優(yōu)化鑄鋼件工藝
成分檢測:嚴格控制鑄鋼的成分,確保成分符合要求。
熔煉溫度控制:嚴格控制熔煉溫度,確保金屬液的流動性和純凈度。
澆注速度控制:合理控制澆注速度,避免氣泡和夾渣的產(chǎn)生。
冷卻速度控制:通過調(diào)整冷卻介質(zhì)和冷卻時間,精確控制冷卻速度。
熱處理優(yōu)化:通過適當?shù)臒崽幚?,改善鑄件的力學性能,減少內(nèi)應(yīng)力。
2.優(yōu)化鑄鐵件工藝
成分檢測:嚴格控制鑄鐵的成分,確保成分符合要求。
熔煉溫度控制:嚴格控制熔煉溫度,確保金屬液的流動性和純凈度。
澆注速度控制:合理控制澆注速度,避免氣泡和夾渣的產(chǎn)生。
冷卻速度控制:通過調(diào)整冷卻介質(zhì)和冷卻時間,精確控制冷卻速度。
清理與加工:通過機械清理和噴砂處理,去除鑄件表面的砂子和毛刺。
通過這些措施,該企業(yè)的發(fā)動機缸體鑄造質(zhì)量得到了顯著提升,生產(chǎn)效率也大幅提高。
四、具體問題與解決方法
1.氣孔和夾渣
鑄鋼件
問題描述:鑄鋼件在澆注過程中容易產(chǎn)生氣孔和夾渣,導(dǎo)致鑄件表面和內(nèi)部存在缺陷。
原因分析:
澆注溫度過低:澆注溫度過低會導(dǎo)致金屬液流動性差,容易形成氣孔和夾渣。
澆注速度過快:澆注速度過快會導(dǎo)致金屬液沖擊砂模,產(chǎn)生氣孔和夾渣。
砂模透氣性差:砂模透氣性差會導(dǎo)致氣體無法及時排出,形成氣孔。
解決方法:
提高澆注溫度:確保澆注溫度在1500℃以上,提高金屬液的流動性。
控制澆注速度:合理控制澆注速度,避免金屬液沖擊砂模。
優(yōu)化砂模透氣性:選擇透氣性好的砂子,提高砂模的透氣性。
鑄鐵件
問題描述:鑄鐵件在澆注過程中容易產(chǎn)生氣孔和夾渣,導(dǎo)致鑄件表面和內(nèi)部存在缺陷。
原因分析:
澆注溫度過低:澆注溫度過低會導(dǎo)致金屬液流動性差,容易形成氣孔和夾渣。
澆注速度過快:澆注速度過快會導(dǎo)致金屬液沖擊砂模,產(chǎn)生氣孔和夾渣。
砂模透氣性差:砂模透氣性差會導(dǎo)致氣體無法及時排出,形成氣孔。
解決方法:
提高澆注溫度:確保澆注溫度在1200℃~1400℃之間,提高金屬液的流動性。
控制澆注速度:合理控制澆注速度,避免金屬液沖擊砂模。
優(yōu)化砂模透氣性:選擇透氣性好的砂子,提高砂模的透氣性。
2.裂紋
鑄鋼件
問題描述:鑄鋼件在冷卻過程中容易產(chǎn)生裂紋,導(dǎo)致鑄件報廢。
原因分析:
冷卻速度過快:冷卻速度過快會導(dǎo)致鑄件內(nèi)部應(yīng)力增大,產(chǎn)生裂紋。
砂模強度不夠:砂模強度不夠會導(dǎo)致鑄件在冷卻過程中變形,產(chǎn)生裂紋。
熱處理不當:熱處理溫度和時間不合理,導(dǎo)致鑄件內(nèi)部應(yīng)力不均勻。
解決方法:
控制冷卻速度:通過調(diào)整冷卻介質(zhì)和冷卻時間,精確控制冷卻速度。
提高砂模強度:選擇強度高的砂子,提高砂模的強度。
優(yōu)化熱處理:合理設(shè)置熱處理溫度和時間,消除鑄件內(nèi)部應(yīng)力。
鑄鐵件
問題描述:鑄鐵件在冷卻過程中容易產(chǎn)生裂紋,導(dǎo)致鑄件報廢。
原因分析:
冷卻速度過快:冷卻速度過快會導(dǎo)致鑄件內(nèi)部應(yīng)力增大,產(chǎn)生裂紋。
砂模強度不夠:砂模強度不夠會導(dǎo)致鑄件在冷卻過程中變形,產(chǎn)生裂紋。
熱處理不當:熱處理溫度和時間不合理,導(dǎo)致鑄件內(nèi)部應(yīng)力不均勻。
解決方法:
控制冷卻速度:通過調(diào)整冷卻介質(zhì)和冷卻時間,精確控制冷卻速度。
提高砂模強度:選擇強度高的砂子,提高砂模的強度。
優(yōu)化熱處理:合理設(shè)置熱處理溫度和時間,消除鑄件內(nèi)部應(yīng)力。
3.尺寸偏差
鑄鋼件
問題描述:鑄鋼件在加工過程中容易出現(xiàn)尺寸偏差,導(dǎo)致鑄件不符合圖紙要求。
原因分析:
模具尺寸精度不高:模具尺寸精度不高會導(dǎo)致鑄件尺寸偏差。
澆注過程控制不當:澆注過程中的溫度和速度控制不當,導(dǎo)致鑄件尺寸偏差。
冷卻過程控制不當:冷卻過程中的溫度和時間控制不當,導(dǎo)致鑄件尺寸偏差。
解決方法:
提高模具精度:通過三維建模和精密加工,提高模具尺寸精度。
嚴格控制澆注過程:合理控制澆注溫度和速度,避免尺寸偏差。
嚴格控制冷卻過程:合理控制冷卻溫度和時間,避免尺寸偏差。
鑄鐵件
問題描述:鑄鐵件在加工過程中容易出現(xiàn)尺寸偏差,導(dǎo)致鑄件不符合圖紙要求。
原因分析:
模具尺寸精度不高:模具尺寸精度不高會導(dǎo)致鑄件尺寸偏差。
澆注過程控制不當:澆注過程中的溫度和速度控制不當,導(dǎo)致鑄件尺寸偏差。
冷卻過程控制不當:冷卻過程中的溫度和時間控制不當,導(dǎo)致鑄件尺寸偏差。
解決方法:
提高模具精度:通過三維建模和精密加工,提高模具尺寸精度。
嚴格控制澆注過程:合理控制澆注溫度和速度,避免尺寸偏差。
嚴格控制冷卻過程:合理控制冷卻溫度和時間,避免尺寸偏差。
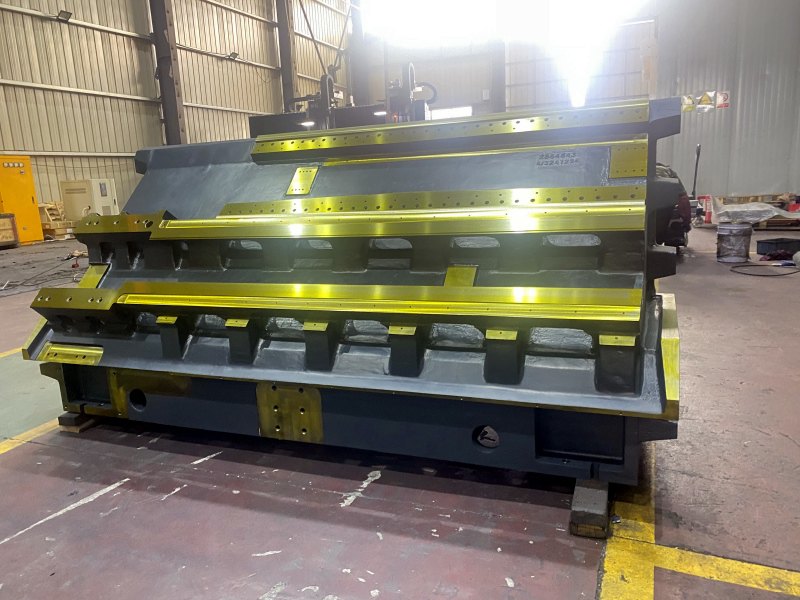
4.表面粗糙
鑄鋼件
問題描述:鑄鋼件表面粗糙度較高,需要進行后續(xù)加工。
原因分析:
砂模表面粗糙:砂模表面粗糙會導(dǎo)致鑄件表面粗糙。
澆注過程控制不當:澆注過程中的溫度和速度控制不當,導(dǎo)致鑄件表面粗糙。
冷卻過程控制不當:冷卻過程中的溫度和時間控制不當,導(dǎo)致鑄件表面粗糙。
解決方法:
提高砂模表面質(zhì)量:選擇表面光滑的砂子,提高砂模表面質(zhì)量。
嚴格控制澆注過程:合理控制澆注溫度和速度,避免表面粗糙。
嚴格控制冷卻過程:合理控制冷卻溫度和時間,避免表面粗糙。
鑄鐵件
問題描述:鑄鐵件表面粗糙度較高,需要進行后續(xù)加工。
原因分析:
砂模表面粗糙:砂模表面粗糙會導(dǎo)致鑄件表面粗糙。
澆注過程控制不當:澆注過程中的溫度和速度控制不當,導(dǎo)致鑄件表面粗糙。
冷卻過程控制不當:冷卻過程中的溫度和時間控制不當,導(dǎo)致鑄件表面粗糙。
解決方法:
提高砂模表面質(zhì)量:選擇表面光滑的砂子,提高砂模表面質(zhì)量。
嚴格控制澆注過程:合理控制澆注溫度和速度,避免表面粗糙。
嚴格控制冷卻過程:合理控制冷卻溫度和時間,避免表面粗糙。
5.機械性能不足
鑄鋼件
問題描述:鑄鋼件在使用過程中機械性能不足,導(dǎo)致使用壽命縮短。
原因分析:
成分控制不當:鑄鋼成分控制不當,導(dǎo)致機械性能不足。
熱處理不當:熱處理溫度和時間不合理,導(dǎo)致機械性能不足。
冷卻過程控制不當:冷卻過程中的溫度和時間控制不當,導(dǎo)致機械性能不足。
解決方法:
嚴格控制成分:通過成分檢測,確保鑄鋼成分符合要求。
優(yōu)化熱處理:合理設(shè)置熱處理溫度和時間,提高機械性能。
嚴格控制冷卻過程:合理控制冷卻溫度和時間,提高機械性能。
鑄鐵件
問題描述:鑄鐵件在使用過程中機械性能不足,導(dǎo)致使用壽命縮短。
原因分析:
成分控制不當:鑄鐵成分控制不當,導(dǎo)致機械性能不足。
熱處理不當:熱處理溫度和時間不合理,導(dǎo)致機械性能不足。
冷卻過程控制不當:冷卻過程中的溫度和時間控制不當,導(dǎo)致機械性能不足。
解決方法:
嚴格控制成分:通過成分檢測,確保鑄鐵成分符合要求。
優(yōu)化熱處理:合理設(shè)置熱處理溫度和時間,提高機械性能。
嚴格控制冷卻過程:合理控制冷卻溫度和時間,提高機械性能。
6.澆注不足
鑄鋼件
問題描述:鑄鋼件在澆注過程中出現(xiàn)澆注不足的現(xiàn)象,導(dǎo)致鑄件局部未充滿。
原因分析:
澆注溫度過低:澆注溫度過低,金屬液流動性差,導(dǎo)致澆注不足。
澆注速度過慢:澆注速度過慢,導(dǎo)致金屬液未能及時填充模具。
澆注系統(tǒng)設(shè)計不合理:澆注系統(tǒng)設(shè)計不合理,導(dǎo)致金屬液流動不暢。
解決方法:
提高澆注溫度:確保澆注溫度在1500℃以上,提高金屬液的流動性。
加快澆注速度:合理控制澆注速度,確保金屬液及時填充模具。
優(yōu)化澆注系統(tǒng)設(shè)計:重新設(shè)計澆注系統(tǒng),確保金屬液順暢流動。
鑄鐵件
問題描述:鑄鐵件在澆注過程中出現(xiàn)澆注不足的現(xiàn)象,導(dǎo)致鑄件局部未充滿。
原因分析:
澆注溫度過低:澆注溫度過低,金屬液流動性差,導(dǎo)致澆注不足。
澆注速度過慢:澆注速度過慢,導(dǎo)致金屬液未能及時填充模具。
澆注系統(tǒng)設(shè)計不合理:澆注系統(tǒng)設(shè)計不合理,導(dǎo)致金屬液流動不暢。
解決方法:
提高澆注溫度:確保澆注溫度在1200℃~1400℃之間,提高金屬液的流動性。
加快澆注速度:合理控制澆注速度,確保金屬液及時填充模具。
優(yōu)化澆注系統(tǒng)設(shè)計:重新設(shè)計澆注系統(tǒng),確保金屬液順暢流動。
7.縮孔和縮松
鑄鋼件
問題描述:鑄鋼件在冷卻過程中容易產(chǎn)生縮孔和縮松,導(dǎo)致鑄件內(nèi)部存在缺陷。
原因分析:
冷卻速度不均勻:冷卻速度不均勻,導(dǎo)致鑄件內(nèi)部產(chǎn)生縮孔和縮松。
澆注系統(tǒng)設(shè)計不合理:澆注系統(tǒng)設(shè)計不合理,導(dǎo)致金屬液流動不暢,局部冷卻速度過快。
澆注溫度控制不當:澆注溫度控制不當,導(dǎo)致金屬液流動性差。
解決方法:
優(yōu)化冷卻系統(tǒng):通過調(diào)整冷卻介質(zhì)和冷卻時間,確保冷卻速度均勻。
優(yōu)化澆注系統(tǒng)設(shè)計:重新設(shè)計澆注系統(tǒng),確保金屬液順暢流動。
嚴格控制澆注溫度:確保澆注溫度在1500℃以上,提高金屬液的流動性。
鑄鐵件
問題描述:鑄鐵件在冷卻過程中容易產(chǎn)生縮孔和縮松,導(dǎo)致鑄件內(nèi)部存在缺陷。
原因分析:
冷卻速度不均勻:冷卻速度不均勻,導(dǎo)致鑄件內(nèi)部產(chǎn)生縮孔和縮松。
澆注系統(tǒng)設(shè)計不合理:澆注系統(tǒng)設(shè)計不合理,導(dǎo)致金屬液流動不暢,局部冷卻速度過快。
澆注溫度控制不當:澆注溫度控制不當,導(dǎo)致金屬液流動性差。
解決方法:
優(yōu)化冷卻系統(tǒng):通過調(diào)整冷卻介質(zhì)和冷卻時間,確保冷卻速度均勻。
優(yōu)化澆注系統(tǒng)設(shè)計:重新設(shè)計澆注系統(tǒng),確保金屬液順暢流動。
嚴格控制澆注溫度:確保澆注溫度在1200℃~1400℃之間,提高金屬液的流動性。
8.偏析
鑄鋼件
問題描述:鑄鋼件在冷卻過程中容易出現(xiàn)成分偏析,導(dǎo)致鑄件性能不均勻。
原因分析:
澆注速度過快:澆注速度過快,導(dǎo)致金屬液成分分布不均。
冷卻速度過快:冷卻速度過快,導(dǎo)致鑄件內(nèi)部成分分布不均。
澆注系統(tǒng)設(shè)計不合理:澆注系統(tǒng)設(shè)計不合理,導(dǎo)致金屬液流動不均。
解決方法:
控制澆注速度:合理控制澆注速度,確保金屬液均勻流動。
控制冷卻速度:通過調(diào)整冷卻介質(zhì)和冷卻時間,確保冷卻速度均勻。
優(yōu)化澆注系統(tǒng)設(shè)計:重新設(shè)計澆注系統(tǒng),確保金屬液均勻流動。
鑄鐵件
問題描述:鑄鐵件在冷卻過程中容易出現(xiàn)成分偏析,導(dǎo)致鑄件性能不均勻。
原因分析:
澆注速度過快:澆注速度過快,導(dǎo)致金屬液成分分布不均。
冷卻速度過快:冷卻速度過快,導(dǎo)致鑄件內(nèi)部成分分布不均。
澆注系統(tǒng)設(shè)計不合理:澆注系統(tǒng)設(shè)計不合理,導(dǎo)致金屬液流動不均。
解決方法:
控制澆注速度:合理控制澆注速度,確保金屬液均勻流動。
控制冷卻速度:通過調(diào)整冷卻介質(zhì)和冷卻時間,確保冷卻速度均勻。
優(yōu)化澆注系統(tǒng)設(shè)計:重新設(shè)計澆注系統(tǒng),確保金屬液均勻流動。
9.熱裂紋
鑄鋼件
問題描述:鑄鋼件在冷卻過程中容易產(chǎn)生熱裂紋,導(dǎo)致鑄件報廢。
原因分析:
冷卻速度過快:冷卻速度過快,導(dǎo)致鑄件內(nèi)部應(yīng)力增大,產(chǎn)生熱裂紋。
砂模強度不夠:砂模強度不夠,導(dǎo)致鑄件在冷卻過程中變形,產(chǎn)生熱裂紋。
熱處理不當:熱處理溫度和時間不合理,導(dǎo)致鑄件內(nèi)部應(yīng)力不均勻。
解決方法:
控制冷卻速度:通過調(diào)整冷卻介質(zhì)和冷卻時間,精確控制冷卻速度。
提高砂模強度:選擇強度高的砂子,提高砂模的強度。
優(yōu)化熱處理:合理設(shè)置熱處理溫度和時間,消除鑄件內(nèi)部應(yīng)力。
鑄鐵件
問題描述:鑄鐵件在冷卻過程中容易產(chǎn)生熱裂紋,導(dǎo)致鑄件報廢。
原因分析:
冷卻速度過快:冷卻速度過快,導(dǎo)致鑄件內(nèi)部應(yīng)力增大,產(chǎn)生熱裂紋。
砂模強度不夠:砂模強度不夠,導(dǎo)致鑄件在冷卻過程中變形,產(chǎn)生熱裂紋。
熱處理不當:熱處理溫度和時間不合理,導(dǎo)致鑄件內(nèi)部應(yīng)力不均勻。
解決方法:
控制冷卻速度:通過調(diào)整冷卻介質(zhì)和冷卻時間,精確控制冷卻速度。
提高砂模強度:選擇強度高的砂子,提高砂模的強度。
優(yōu)化熱處理:合理設(shè)置熱處理溫度和時間,消除鑄件內(nèi)部應(yīng)力。
10.殘余應(yīng)力
鑄鋼件
問題描述:鑄鋼件在冷卻過程中容易產(chǎn)生殘余應(yīng)力,導(dǎo)致鑄件變形或開裂。
原因分析:
冷卻速度過快:冷卻速度過快,導(dǎo)致鑄件內(nèi)部應(yīng)力增大。
熱處理不當:熱處理溫度和時間不合理,導(dǎo)致鑄件內(nèi)部應(yīng)力不均勻。
澆注系統(tǒng)設(shè)計不合理:澆注系統(tǒng)設(shè)計不合理,導(dǎo)致金屬液流動不均,局部應(yīng)力集中。
解決方法:
控制冷卻速度:通過調(diào)整冷卻介質(zhì)和冷卻時間,精確控制冷卻速度。
優(yōu)化熱處理:合理設(shè)置熱處理溫度和時間,消除鑄件內(nèi)部應(yīng)力。
優(yōu)化澆注系統(tǒng)設(shè)計:重新設(shè)計澆注系統(tǒng),確保金屬液均勻流動。
鑄鐵件
問題描述:鑄鐵件在冷卻過程中容易產(chǎn)生殘余應(yīng)力,導(dǎo)致鑄件變形或開裂。
原因分析:
冷卻速度過快:冷卻速度過快,導(dǎo)致鑄件內(nèi)部應(yīng)力增大。
熱處理不當:熱處理溫度和時間不合理,導(dǎo)致鑄件內(nèi)部應(yīng)力不均勻。
澆注系統(tǒng)設(shè)計不合理:澆注系統(tǒng)設(shè)計不合理,導(dǎo)致金屬液流動不均,局部應(yīng)力集中。
解決方法:
控制冷卻速度:通過調(diào)整冷卻介質(zhì)和冷卻時間,精確控制冷卻速度。
優(yōu)化熱處理:合理設(shè)置熱處理溫度和時間,消除鑄件內(nèi)部應(yīng)力。
優(yōu)化澆注系統(tǒng)設(shè)計:重新設(shè)計澆注系統(tǒng),確保金屬液均勻流動。
以上十點是鑄鋼件與鑄鐵件在鑄造過程中會遇到多種常見問題,問題包括氣孔和夾渣、裂紋、尺寸偏差、表面粗糙、澆注不足、縮孔和縮松、偏析、熱裂紋、粘砂等。下期我們繼續(xù)給大家介紹鑄鋼件與鑄鐵件遇到的常見問題,通過對這些問題的原因進行詳細分析,并采取相應(yīng)的解決方法,可以有效提高鑄件的質(zhì)量和性能。
通過本文的詳細分析,希望相關(guān)企業(yè)和技術(shù)人員能夠更好地理解和應(yīng)對鑄鋼件與鑄鐵件在鑄造過程中遇到的問題,確保鑄件的質(zhì)量和生產(chǎn)效率。
一、鑄鋼件的常見問題及其解決方法
1.氣孔和夾渣
問題描述:鑄鋼件在澆注過程中容易產(chǎn)生氣孔和夾渣,導(dǎo)致鑄件表面和內(nèi)部存在缺陷。
原因分析:
澆注溫度過低:澆注溫度過低會導(dǎo)致金屬液流動性差,容易形成氣孔和夾渣。
澆注速度過快:澆注速度過快會導(dǎo)致金屬液沖擊砂模,產(chǎn)生氣孔和夾渣。
砂模透氣性差:砂模透氣性差會導(dǎo)致氣體無法及時排出,形成氣孔。
解決方法:
提高澆注溫度:確保澆注溫度在1500℃以上,提高金屬液的流動性。
控制澆注速度:合理控制澆注速度,避免金屬液沖擊砂模。
優(yōu)化砂模透氣性:選擇透氣性好的砂子,提高砂模的透氣性。
2.裂紋
問題描述:鑄鋼件在冷卻過程中容易產(chǎn)生裂紋,導(dǎo)致鑄件報廢。
原因分析:
冷卻速度過快:冷卻速度過快會導(dǎo)致鑄件內(nèi)部應(yīng)力增大,產(chǎn)生裂紋。
砂模強度不夠:砂模強度不夠會導(dǎo)致鑄件在冷卻過程中變形,產(chǎn)生裂紋。
熱處理不當:熱處理溫度和時間不合理,導(dǎo)致鑄件內(nèi)部應(yīng)力不均勻。
解決方法:
控制冷卻速度:通過調(diào)整冷卻介質(zhì)和冷卻時間,精確控制冷卻速度。
提高砂模強度:選擇強度高的砂子,提高砂模的強度。
優(yōu)化熱處理:合理設(shè)置熱處理溫度和時間,消除鑄件內(nèi)部應(yīng)力。
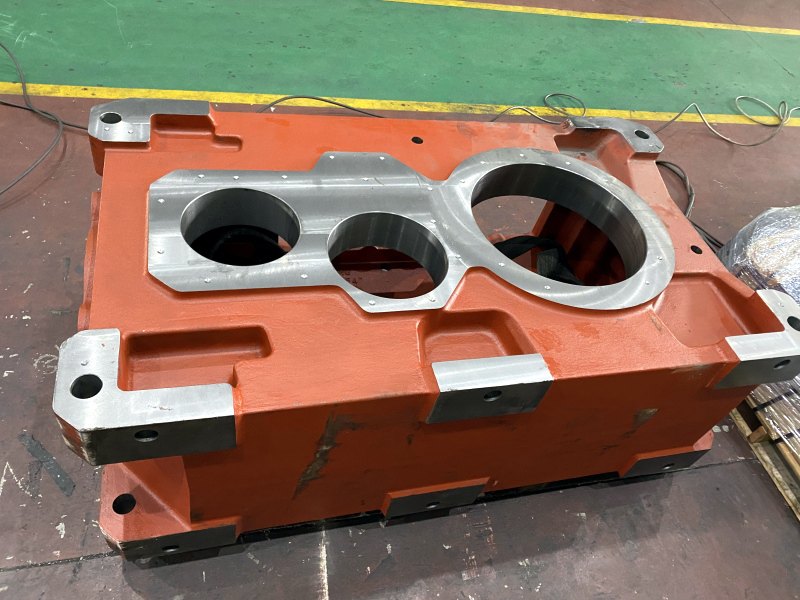
問題描述:鑄鋼件在加工過程中容易出現(xiàn)尺寸偏差,導(dǎo)致鑄件不符合圖紙要求。
原因分析:
模具尺寸精度不高:模具尺寸精度不高會導(dǎo)致鑄件尺寸偏差。
澆注過程控制不當:澆注過程中的溫度和速度控制不當,導(dǎo)致鑄件尺寸偏差。
冷卻過程控制不當:冷卻過程中的溫度和時間控制不當,導(dǎo)致鑄件尺寸偏差。
解決方法:
提高模具精度:通過三維建模和精密加工,提高模具尺寸精度。
嚴格控制澆注過程:合理控制澆注溫度和速度,避免尺寸偏差。
嚴格控制冷卻過程:合理控制冷卻溫度和時間,避免尺寸偏差。
4.表面粗糙
問題描述:鑄鋼件表面粗糙度較高,需要進行后續(xù)加工。
原因分析:
砂模表面粗糙:砂模表面粗糙會導(dǎo)致鑄件表面粗糙。
澆注過程控制不當:澆注過程中的溫度和速度控制不當,導(dǎo)致鑄件表面粗糙。
冷卻過程控制不當:冷卻過程中的溫度和時間控制不當,導(dǎo)致鑄件表面粗糙。
解決方法:
提高砂模表面質(zhì)量:選擇表面光滑的砂子,提高砂模表面質(zhì)量。
嚴格控制澆注過程:合理控制澆注溫度和速度,避免表面粗糙。
嚴格控制冷卻過程:合理控制冷卻溫度和時間,避免表面粗糙。
5.機械性能不足
問題描述:鑄鋼件在使用過程中機械性能不足,導(dǎo)致使用壽命縮短。
原因分析:
成分控制不當:鑄鋼成分控制不當,導(dǎo)致機械性能不足。
熱處理不當:熱處理溫度和時間不合理,導(dǎo)致機械性能不足。
冷卻過程控制不當:冷卻過程中的溫度和時間控制不當,導(dǎo)致機械性能不足。
解決方法:
嚴格控制成分:通過成分檢測,確保鑄鋼成分符合要求。
優(yōu)化熱處理:合理設(shè)置熱處理溫度和時間,提高機械性能。
嚴格控制冷卻過程:合理控制冷卻溫度和時間,提高機械性能。
二、鑄鐵件的常見問題及其解決方法
1.氣孔和夾渣
問題描述:鑄鐵件在澆注過程中容易產(chǎn)生氣孔和夾渣,導(dǎo)致鑄件表面和內(nèi)部存在缺陷。
原因分析:
澆注溫度過低:澆注溫度過低會導(dǎo)致金屬液流動性差,容易形成氣孔和夾渣。
澆注速度過快:澆注速度過快會導(dǎo)致金屬液沖擊砂模,產(chǎn)生氣孔和夾渣。
砂模透氣性差:砂模透氣性差會導(dǎo)致氣體無法及時排出,形成氣孔。
解決方法:
提高澆注溫度:確保澆注溫度在1200℃~1400℃之間,提高金屬液的流動性。
控制澆注速度:合理控制澆注速度,避免金屬液沖擊砂模。
優(yōu)化砂模透氣性:選擇透氣性好的砂子,提高砂模的透氣性。
2.裂紋
問題描述:鑄鐵件在冷卻過程中容易產(chǎn)生裂紋,導(dǎo)致鑄件報廢。
原因分析:
冷卻速度過快:冷卻速度過快會導(dǎo)致鑄件內(nèi)部應(yīng)力增大,產(chǎn)生裂紋。
砂模強度不夠:砂模強度不夠會導(dǎo)致鑄件在冷卻過程中變形,產(chǎn)生裂紋。
熱處理不當:熱處理溫度和時間不合理,導(dǎo)致鑄件內(nèi)部應(yīng)力不均勻。
解決方法:
控制冷卻速度:通過調(diào)整冷卻介質(zhì)和冷卻時間,精確控制冷卻速度。
提高砂模強度:選擇強度高的砂子,提高砂模的強度。
優(yōu)化熱處理:合理設(shè)置熱處理溫度和時間,消除鑄件內(nèi)部應(yīng)力。
3.尺寸偏差
問題描述:鑄鐵件在加工過程中容易出現(xiàn)尺寸偏差,導(dǎo)致鑄件不符合圖紙要求。
原因分析:
模具尺寸精度不高:模具尺寸精度不高會導(dǎo)致鑄件尺寸偏差。
澆注過程控制不當:澆注過程中的溫度和速度控制不當,導(dǎo)致鑄件尺寸偏差。
冷卻過程控制不當:冷卻過程中的溫度和時間控制不當,導(dǎo)致鑄件尺寸偏差。
解決方法:
提高模具精度:通過三維建模和精密加工,提高模具尺寸精度。
嚴格控制澆注過程:合理控制澆注溫度和速度,避免尺寸偏差。
嚴格控制冷卻過程:合理控制冷卻溫度和時間,避免尺寸偏差。
4.表面粗糙
問題描述:鑄鐵件表面粗糙度較高,需要進行后續(xù)加工。
原因分析:
砂模表面粗糙:砂模表面粗糙會導(dǎo)致鑄件表面粗糙。
澆注過程控制不當:澆注過程中的溫度和速度控制不當,導(dǎo)致鑄件表面粗糙。
冷卻過程控制不當:冷卻過程中的溫度和時間控制不當,導(dǎo)致鑄件表面粗糙。
解決方法:
提高砂模表面質(zhì)量:選擇表面光滑的砂子,提高砂模表面質(zhì)量。
嚴格控制澆注過程:合理控制澆注溫度和速度,避免表面粗糙。
嚴格控制冷卻過程:合理控制冷卻溫度和時間,避免表面粗糙。
5.機械性能不足
問題描述:鑄鐵件在使用過程中機械性能不足,導(dǎo)致使用壽命縮短。
原因分析:
成分控制不當:鑄鐵成分控制不當,導(dǎo)致機械性能不足。
熱處理不當:熱處理溫度和時間不合理,導(dǎo)致機械性能不足。
冷卻過程控制不當:冷卻過程中的溫度和時間控制不當,導(dǎo)致機械性能不足。
解決方法:
嚴格控制成分:通過成分檢測,確保鑄鐵成分符合要求。
優(yōu)化熱處理:合理設(shè)置熱處理溫度和時間,提高機械性能。
嚴格控制冷卻過程:合理控制冷卻溫度和時間,提高機械性能。
三、案例分析
以某機械制造企業(yè)的發(fā)動機缸體生產(chǎn)為例,該企業(yè)在鑄鋼件和鑄鐵件的生產(chǎn)過程中遇到了鑄件質(zhì)量不穩(wěn)定的問題。通過以下措施,企業(yè)解決了這些問題:
1.優(yōu)化鑄鋼件工藝
成分檢測:嚴格控制鑄鋼的成分,確保成分符合要求。
熔煉溫度控制:嚴格控制熔煉溫度,確保金屬液的流動性和純凈度。
澆注速度控制:合理控制澆注速度,避免氣泡和夾渣的產(chǎn)生。
冷卻速度控制:通過調(diào)整冷卻介質(zhì)和冷卻時間,精確控制冷卻速度。
熱處理優(yōu)化:通過適當?shù)臒崽幚?,改善鑄件的力學性能,減少內(nèi)應(yīng)力。
2.優(yōu)化鑄鐵件工藝
成分檢測:嚴格控制鑄鐵的成分,確保成分符合要求。
熔煉溫度控制:嚴格控制熔煉溫度,確保金屬液的流動性和純凈度。
澆注速度控制:合理控制澆注速度,避免氣泡和夾渣的產(chǎn)生。
冷卻速度控制:通過調(diào)整冷卻介質(zhì)和冷卻時間,精確控制冷卻速度。
清理與加工:通過機械清理和噴砂處理,去除鑄件表面的砂子和毛刺。
通過這些措施,該企業(yè)的發(fā)動機缸體鑄造質(zhì)量得到了顯著提升,生產(chǎn)效率也大幅提高。
四、具體問題與解決方法
1.氣孔和夾渣
鑄鋼件
問題描述:鑄鋼件在澆注過程中容易產(chǎn)生氣孔和夾渣,導(dǎo)致鑄件表面和內(nèi)部存在缺陷。
原因分析:
澆注溫度過低:澆注溫度過低會導(dǎo)致金屬液流動性差,容易形成氣孔和夾渣。
澆注速度過快:澆注速度過快會導(dǎo)致金屬液沖擊砂模,產(chǎn)生氣孔和夾渣。
砂模透氣性差:砂模透氣性差會導(dǎo)致氣體無法及時排出,形成氣孔。
解決方法:
提高澆注溫度:確保澆注溫度在1500℃以上,提高金屬液的流動性。
控制澆注速度:合理控制澆注速度,避免金屬液沖擊砂模。
優(yōu)化砂模透氣性:選擇透氣性好的砂子,提高砂模的透氣性。
鑄鐵件
問題描述:鑄鐵件在澆注過程中容易產(chǎn)生氣孔和夾渣,導(dǎo)致鑄件表面和內(nèi)部存在缺陷。
原因分析:
澆注溫度過低:澆注溫度過低會導(dǎo)致金屬液流動性差,容易形成氣孔和夾渣。
澆注速度過快:澆注速度過快會導(dǎo)致金屬液沖擊砂模,產(chǎn)生氣孔和夾渣。
砂模透氣性差:砂模透氣性差會導(dǎo)致氣體無法及時排出,形成氣孔。
解決方法:
提高澆注溫度:確保澆注溫度在1200℃~1400℃之間,提高金屬液的流動性。
控制澆注速度:合理控制澆注速度,避免金屬液沖擊砂模。
優(yōu)化砂模透氣性:選擇透氣性好的砂子,提高砂模的透氣性。
2.裂紋
鑄鋼件
問題描述:鑄鋼件在冷卻過程中容易產(chǎn)生裂紋,導(dǎo)致鑄件報廢。
原因分析:
冷卻速度過快:冷卻速度過快會導(dǎo)致鑄件內(nèi)部應(yīng)力增大,產(chǎn)生裂紋。
砂模強度不夠:砂模強度不夠會導(dǎo)致鑄件在冷卻過程中變形,產(chǎn)生裂紋。
熱處理不當:熱處理溫度和時間不合理,導(dǎo)致鑄件內(nèi)部應(yīng)力不均勻。
解決方法:
控制冷卻速度:通過調(diào)整冷卻介質(zhì)和冷卻時間,精確控制冷卻速度。
提高砂模強度:選擇強度高的砂子,提高砂模的強度。
優(yōu)化熱處理:合理設(shè)置熱處理溫度和時間,消除鑄件內(nèi)部應(yīng)力。
鑄鐵件
問題描述:鑄鐵件在冷卻過程中容易產(chǎn)生裂紋,導(dǎo)致鑄件報廢。
原因分析:
冷卻速度過快:冷卻速度過快會導(dǎo)致鑄件內(nèi)部應(yīng)力增大,產(chǎn)生裂紋。
砂模強度不夠:砂模強度不夠會導(dǎo)致鑄件在冷卻過程中變形,產(chǎn)生裂紋。
熱處理不當:熱處理溫度和時間不合理,導(dǎo)致鑄件內(nèi)部應(yīng)力不均勻。
解決方法:
控制冷卻速度:通過調(diào)整冷卻介質(zhì)和冷卻時間,精確控制冷卻速度。
提高砂模強度:選擇強度高的砂子,提高砂模的強度。
優(yōu)化熱處理:合理設(shè)置熱處理溫度和時間,消除鑄件內(nèi)部應(yīng)力。
3.尺寸偏差
鑄鋼件
問題描述:鑄鋼件在加工過程中容易出現(xiàn)尺寸偏差,導(dǎo)致鑄件不符合圖紙要求。
原因分析:
模具尺寸精度不高:模具尺寸精度不高會導(dǎo)致鑄件尺寸偏差。
澆注過程控制不當:澆注過程中的溫度和速度控制不當,導(dǎo)致鑄件尺寸偏差。
冷卻過程控制不當:冷卻過程中的溫度和時間控制不當,導(dǎo)致鑄件尺寸偏差。
解決方法:
提高模具精度:通過三維建模和精密加工,提高模具尺寸精度。
嚴格控制澆注過程:合理控制澆注溫度和速度,避免尺寸偏差。
嚴格控制冷卻過程:合理控制冷卻溫度和時間,避免尺寸偏差。
鑄鐵件
問題描述:鑄鐵件在加工過程中容易出現(xiàn)尺寸偏差,導(dǎo)致鑄件不符合圖紙要求。
原因分析:
模具尺寸精度不高:模具尺寸精度不高會導(dǎo)致鑄件尺寸偏差。
澆注過程控制不當:澆注過程中的溫度和速度控制不當,導(dǎo)致鑄件尺寸偏差。
冷卻過程控制不當:冷卻過程中的溫度和時間控制不當,導(dǎo)致鑄件尺寸偏差。
解決方法:
提高模具精度:通過三維建模和精密加工,提高模具尺寸精度。
嚴格控制澆注過程:合理控制澆注溫度和速度,避免尺寸偏差。
嚴格控制冷卻過程:合理控制冷卻溫度和時間,避免尺寸偏差。
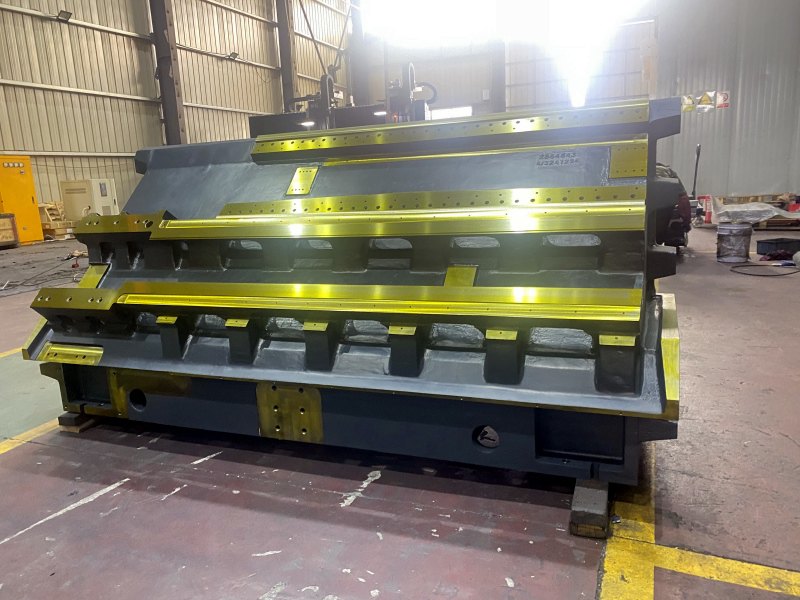
4.表面粗糙
鑄鋼件
問題描述:鑄鋼件表面粗糙度較高,需要進行后續(xù)加工。
原因分析:
砂模表面粗糙:砂模表面粗糙會導(dǎo)致鑄件表面粗糙。
澆注過程控制不當:澆注過程中的溫度和速度控制不當,導(dǎo)致鑄件表面粗糙。
冷卻過程控制不當:冷卻過程中的溫度和時間控制不當,導(dǎo)致鑄件表面粗糙。
解決方法:
提高砂模表面質(zhì)量:選擇表面光滑的砂子,提高砂模表面質(zhì)量。
嚴格控制澆注過程:合理控制澆注溫度和速度,避免表面粗糙。
嚴格控制冷卻過程:合理控制冷卻溫度和時間,避免表面粗糙。
鑄鐵件
問題描述:鑄鐵件表面粗糙度較高,需要進行后續(xù)加工。
原因分析:
砂模表面粗糙:砂模表面粗糙會導(dǎo)致鑄件表面粗糙。
澆注過程控制不當:澆注過程中的溫度和速度控制不當,導(dǎo)致鑄件表面粗糙。
冷卻過程控制不當:冷卻過程中的溫度和時間控制不當,導(dǎo)致鑄件表面粗糙。
解決方法:
提高砂模表面質(zhì)量:選擇表面光滑的砂子,提高砂模表面質(zhì)量。
嚴格控制澆注過程:合理控制澆注溫度和速度,避免表面粗糙。
嚴格控制冷卻過程:合理控制冷卻溫度和時間,避免表面粗糙。
5.機械性能不足
鑄鋼件
問題描述:鑄鋼件在使用過程中機械性能不足,導(dǎo)致使用壽命縮短。
原因分析:
成分控制不當:鑄鋼成分控制不當,導(dǎo)致機械性能不足。
熱處理不當:熱處理溫度和時間不合理,導(dǎo)致機械性能不足。
冷卻過程控制不當:冷卻過程中的溫度和時間控制不當,導(dǎo)致機械性能不足。
解決方法:
嚴格控制成分:通過成分檢測,確保鑄鋼成分符合要求。
優(yōu)化熱處理:合理設(shè)置熱處理溫度和時間,提高機械性能。
嚴格控制冷卻過程:合理控制冷卻溫度和時間,提高機械性能。
鑄鐵件
問題描述:鑄鐵件在使用過程中機械性能不足,導(dǎo)致使用壽命縮短。
原因分析:
成分控制不當:鑄鐵成分控制不當,導(dǎo)致機械性能不足。
熱處理不當:熱處理溫度和時間不合理,導(dǎo)致機械性能不足。
冷卻過程控制不當:冷卻過程中的溫度和時間控制不當,導(dǎo)致機械性能不足。
解決方法:
嚴格控制成分:通過成分檢測,確保鑄鐵成分符合要求。
優(yōu)化熱處理:合理設(shè)置熱處理溫度和時間,提高機械性能。
嚴格控制冷卻過程:合理控制冷卻溫度和時間,提高機械性能。
6.澆注不足
鑄鋼件
問題描述:鑄鋼件在澆注過程中出現(xiàn)澆注不足的現(xiàn)象,導(dǎo)致鑄件局部未充滿。
原因分析:
澆注溫度過低:澆注溫度過低,金屬液流動性差,導(dǎo)致澆注不足。
澆注速度過慢:澆注速度過慢,導(dǎo)致金屬液未能及時填充模具。
澆注系統(tǒng)設(shè)計不合理:澆注系統(tǒng)設(shè)計不合理,導(dǎo)致金屬液流動不暢。
解決方法:
提高澆注溫度:確保澆注溫度在1500℃以上,提高金屬液的流動性。
加快澆注速度:合理控制澆注速度,確保金屬液及時填充模具。
優(yōu)化澆注系統(tǒng)設(shè)計:重新設(shè)計澆注系統(tǒng),確保金屬液順暢流動。
鑄鐵件
問題描述:鑄鐵件在澆注過程中出現(xiàn)澆注不足的現(xiàn)象,導(dǎo)致鑄件局部未充滿。
原因分析:
澆注溫度過低:澆注溫度過低,金屬液流動性差,導(dǎo)致澆注不足。
澆注速度過慢:澆注速度過慢,導(dǎo)致金屬液未能及時填充模具。
澆注系統(tǒng)設(shè)計不合理:澆注系統(tǒng)設(shè)計不合理,導(dǎo)致金屬液流動不暢。
解決方法:
提高澆注溫度:確保澆注溫度在1200℃~1400℃之間,提高金屬液的流動性。
加快澆注速度:合理控制澆注速度,確保金屬液及時填充模具。
優(yōu)化澆注系統(tǒng)設(shè)計:重新設(shè)計澆注系統(tǒng),確保金屬液順暢流動。
7.縮孔和縮松
鑄鋼件
問題描述:鑄鋼件在冷卻過程中容易產(chǎn)生縮孔和縮松,導(dǎo)致鑄件內(nèi)部存在缺陷。
原因分析:
冷卻速度不均勻:冷卻速度不均勻,導(dǎo)致鑄件內(nèi)部產(chǎn)生縮孔和縮松。
澆注系統(tǒng)設(shè)計不合理:澆注系統(tǒng)設(shè)計不合理,導(dǎo)致金屬液流動不暢,局部冷卻速度過快。
澆注溫度控制不當:澆注溫度控制不當,導(dǎo)致金屬液流動性差。
解決方法:
優(yōu)化冷卻系統(tǒng):通過調(diào)整冷卻介質(zhì)和冷卻時間,確保冷卻速度均勻。
優(yōu)化澆注系統(tǒng)設(shè)計:重新設(shè)計澆注系統(tǒng),確保金屬液順暢流動。
嚴格控制澆注溫度:確保澆注溫度在1500℃以上,提高金屬液的流動性。
鑄鐵件
問題描述:鑄鐵件在冷卻過程中容易產(chǎn)生縮孔和縮松,導(dǎo)致鑄件內(nèi)部存在缺陷。
原因分析:
冷卻速度不均勻:冷卻速度不均勻,導(dǎo)致鑄件內(nèi)部產(chǎn)生縮孔和縮松。
澆注系統(tǒng)設(shè)計不合理:澆注系統(tǒng)設(shè)計不合理,導(dǎo)致金屬液流動不暢,局部冷卻速度過快。
澆注溫度控制不當:澆注溫度控制不當,導(dǎo)致金屬液流動性差。
解決方法:
優(yōu)化冷卻系統(tǒng):通過調(diào)整冷卻介質(zhì)和冷卻時間,確保冷卻速度均勻。
優(yōu)化澆注系統(tǒng)設(shè)計:重新設(shè)計澆注系統(tǒng),確保金屬液順暢流動。
嚴格控制澆注溫度:確保澆注溫度在1200℃~1400℃之間,提高金屬液的流動性。
8.偏析
鑄鋼件
問題描述:鑄鋼件在冷卻過程中容易出現(xiàn)成分偏析,導(dǎo)致鑄件性能不均勻。
原因分析:
澆注速度過快:澆注速度過快,導(dǎo)致金屬液成分分布不均。
冷卻速度過快:冷卻速度過快,導(dǎo)致鑄件內(nèi)部成分分布不均。
澆注系統(tǒng)設(shè)計不合理:澆注系統(tǒng)設(shè)計不合理,導(dǎo)致金屬液流動不均。
解決方法:
控制澆注速度:合理控制澆注速度,確保金屬液均勻流動。
控制冷卻速度:通過調(diào)整冷卻介質(zhì)和冷卻時間,確保冷卻速度均勻。
優(yōu)化澆注系統(tǒng)設(shè)計:重新設(shè)計澆注系統(tǒng),確保金屬液均勻流動。
鑄鐵件
問題描述:鑄鐵件在冷卻過程中容易出現(xiàn)成分偏析,導(dǎo)致鑄件性能不均勻。
原因分析:
澆注速度過快:澆注速度過快,導(dǎo)致金屬液成分分布不均。
冷卻速度過快:冷卻速度過快,導(dǎo)致鑄件內(nèi)部成分分布不均。
澆注系統(tǒng)設(shè)計不合理:澆注系統(tǒng)設(shè)計不合理,導(dǎo)致金屬液流動不均。
解決方法:
控制澆注速度:合理控制澆注速度,確保金屬液均勻流動。
控制冷卻速度:通過調(diào)整冷卻介質(zhì)和冷卻時間,確保冷卻速度均勻。
優(yōu)化澆注系統(tǒng)設(shè)計:重新設(shè)計澆注系統(tǒng),確保金屬液均勻流動。
9.熱裂紋
鑄鋼件
問題描述:鑄鋼件在冷卻過程中容易產(chǎn)生熱裂紋,導(dǎo)致鑄件報廢。
原因分析:
冷卻速度過快:冷卻速度過快,導(dǎo)致鑄件內(nèi)部應(yīng)力增大,產(chǎn)生熱裂紋。
砂模強度不夠:砂模強度不夠,導(dǎo)致鑄件在冷卻過程中變形,產(chǎn)生熱裂紋。
熱處理不當:熱處理溫度和時間不合理,導(dǎo)致鑄件內(nèi)部應(yīng)力不均勻。
解決方法:
控制冷卻速度:通過調(diào)整冷卻介質(zhì)和冷卻時間,精確控制冷卻速度。
提高砂模強度:選擇強度高的砂子,提高砂模的強度。
優(yōu)化熱處理:合理設(shè)置熱處理溫度和時間,消除鑄件內(nèi)部應(yīng)力。
鑄鐵件
問題描述:鑄鐵件在冷卻過程中容易產(chǎn)生熱裂紋,導(dǎo)致鑄件報廢。
原因分析:
冷卻速度過快:冷卻速度過快,導(dǎo)致鑄件內(nèi)部應(yīng)力增大,產(chǎn)生熱裂紋。
砂模強度不夠:砂模強度不夠,導(dǎo)致鑄件在冷卻過程中變形,產(chǎn)生熱裂紋。
熱處理不當:熱處理溫度和時間不合理,導(dǎo)致鑄件內(nèi)部應(yīng)力不均勻。
解決方法:
控制冷卻速度:通過調(diào)整冷卻介質(zhì)和冷卻時間,精確控制冷卻速度。
提高砂模強度:選擇強度高的砂子,提高砂模的強度。
優(yōu)化熱處理:合理設(shè)置熱處理溫度和時間,消除鑄件內(nèi)部應(yīng)力。
10.殘余應(yīng)力
鑄鋼件
問題描述:鑄鋼件在冷卻過程中容易產(chǎn)生殘余應(yīng)力,導(dǎo)致鑄件變形或開裂。
原因分析:
冷卻速度過快:冷卻速度過快,導(dǎo)致鑄件內(nèi)部應(yīng)力增大。
熱處理不當:熱處理溫度和時間不合理,導(dǎo)致鑄件內(nèi)部應(yīng)力不均勻。
澆注系統(tǒng)設(shè)計不合理:澆注系統(tǒng)設(shè)計不合理,導(dǎo)致金屬液流動不均,局部應(yīng)力集中。
解決方法:
控制冷卻速度:通過調(diào)整冷卻介質(zhì)和冷卻時間,精確控制冷卻速度。
優(yōu)化熱處理:合理設(shè)置熱處理溫度和時間,消除鑄件內(nèi)部應(yīng)力。
優(yōu)化澆注系統(tǒng)設(shè)計:重新設(shè)計澆注系統(tǒng),確保金屬液均勻流動。
鑄鐵件
問題描述:鑄鐵件在冷卻過程中容易產(chǎn)生殘余應(yīng)力,導(dǎo)致鑄件變形或開裂。
原因分析:
冷卻速度過快:冷卻速度過快,導(dǎo)致鑄件內(nèi)部應(yīng)力增大。
熱處理不當:熱處理溫度和時間不合理,導(dǎo)致鑄件內(nèi)部應(yīng)力不均勻。
澆注系統(tǒng)設(shè)計不合理:澆注系統(tǒng)設(shè)計不合理,導(dǎo)致金屬液流動不均,局部應(yīng)力集中。
解決方法:
控制冷卻速度:通過調(diào)整冷卻介質(zhì)和冷卻時間,精確控制冷卻速度。
優(yōu)化熱處理:合理設(shè)置熱處理溫度和時間,消除鑄件內(nèi)部應(yīng)力。
優(yōu)化澆注系統(tǒng)設(shè)計:重新設(shè)計澆注系統(tǒng),確保金屬液均勻流動。
以上十點是鑄鋼件與鑄鐵件在鑄造過程中會遇到多種常見問題,問題包括氣孔和夾渣、裂紋、尺寸偏差、表面粗糙、澆注不足、縮孔和縮松、偏析、熱裂紋、粘砂等。下期我們繼續(xù)給大家介紹鑄鋼件與鑄鐵件遇到的常見問題,通過對這些問題的原因進行詳細分析,并采取相應(yīng)的解決方法,可以有效提高鑄件的質(zhì)量和性能。
通過本文的詳細分析,希望相關(guān)企業(yè)和技術(shù)人員能夠更好地理解和應(yīng)對鑄鋼件與鑄鐵件在鑄造過程中遇到的問題,確保鑄件的質(zhì)量和生產(chǎn)效率。